Gen 49D with Anti-gel: The lubricant factor for Diesel Fuel
- Inhibits corrosion in the fuel tank
- Helps prevent diesel fuel gelling
- Improves low temperature fluidity
- Superior anti-wear protection for fuel pump
- Controls injector deposits and lubrication plungers
Product Information
General Description:
GEN 49D with Anti-Gel is a sulfur-free lubricant designed to synergize with new generation, hydrotreated diesel fuels. It provides complete fuel system protection from corrosion inhibition in the fuel tank, through to lubrication of the fuel pump, deposit control in the injectors and lubricates the compression ring from the fireside of the combustion chamber.
GEN 49D with Anti-Gel provides all diesel engines with extra fuel lubricity, corrosion protection, deposit control and now also improves low temperature fluidity of diesel fuels.
Primary Benefits of GEN 49D with Anti-Gel:
The primary benefit of GEN 49D with Anti-Gel is the restoration of critical diesel fuel lubricity lost through higher severity refining to remove fuel sulfur. At very low application rates, GEN 49D with Anti-Gel dramatically improves diesel fuel lubricity as measured by the BOCLE and HFRR standard tests for fuel lubricity. Improved fuel delivery results in better engine efficiency and longer pump life.
Secondary Benefits of GEN 49D with Anti-Gel:
* Provides optimum lubrication from the fuel pump to the combustion chamber.
* Inhibits corrosion in the fuel tank and fuel lines.
* Improves low temperature fluidity to help prevent gelling.
* Sulfur-free, not alcohol based.
* Controls injector deposits.
* Improves exhaust emission quality.
* Increases equipment availability and extends fuel pump and engine life.
Product Application and Availability:
GEN 49D with Anti-Gel should be added with each fuel fill at a rate of 0.08% (or one part GEN 49D with Anti-Gel added to 1250 parts diesel fuel). This is the equivalent to 8mL per 10L of diesel fuel or one ounce per 10 gallons of diesel fuel. After the initial application, it may be possible, in some warm weather applications, to reduce the treatment rate by 50%. In cold temperatures, 0.08% is required for the anti-gel component to be effective. GEN 49D with Anti-Gel is best applied by partially filling the fuel tank with diesel, adding the correct amount of GEN 49D with Anti-Gel, then topping with diesel fuel.
GEN 49D with Anti-Gel is available in 12 Oz bottles, 1L bottles, 5L & 10L Jugs, 20L Pails and 205L drums
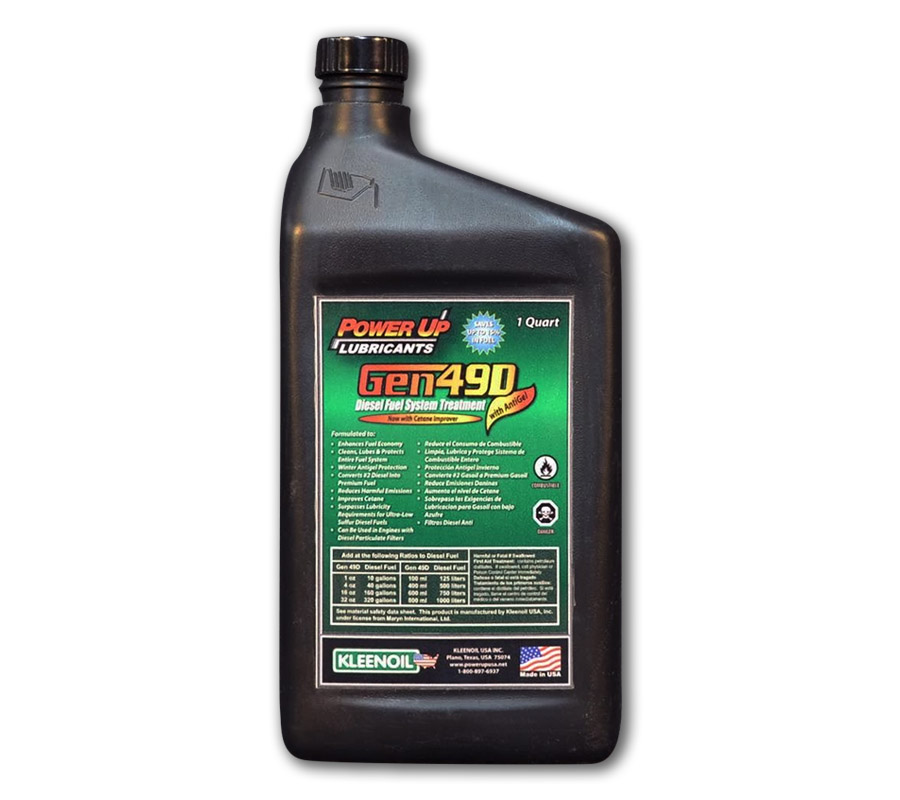
Parkland Oilfield Construction (1983) Ltd. is involved in pipeline installation, batteries, satellites, well site facilities and oilfield plant maintenance. “We can go through 30,000 litres of fuel a day, out of our bulk tankers, and since we have added Gen 49D…we have not had a single fuel pump problem, and the equipment runs much smoother.”
~Steve Ashworth, Parkland Oilfield Construction, Olds, Alberta
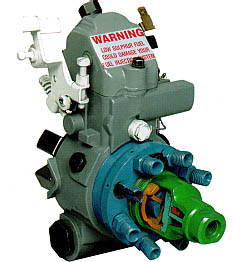
Special Notations:
Cetane Index:
At the recommended application rates, GEN 49D with Anti-Gel does not affect the cetane index of diesel fuel. No effect on the cetane index was determined by ASTM D4737.
Low Temperature:
Power Up GEN 49D with Anti-Gel lowers the pour point of typical #2 diesel fuel by as much as 20oC (36oF).
Ash Content:
Power Up GEN 49D with Anti-Gel does not contain any significant ash.
Application:
GEN 49D with Anti-Gel should be added with each fuel fill at a rate of 0.08% (or one part GEN 49D with Anti-Gel added to 1250 parts diesel fuel). This is the equivalent to 8mL per 10L of diesel fuel or one ounce per 10 gallons of diesel fuel. In summer conditions, the maintenance dosage may be lowered by 50%. In cold temperatures, the regular dosage is required for the anti-gel component to be effective. GEN 49D with Anti-Gel is best applied by partially filling the fuel tank, adding the correct amount of GEN 49D with Anti-Gel, then topping with diesel fuel.
Power Up GEN 49D with Anti-Gel is a sulfur-free lubricant formulated to synergize with new generation, hydrotreated diesel fuels. It provides complete fuel system protection, from corrosion inhibition in the fuel tank, through to lubrication of the fuel pump, deposit control in the injectors and lubrication of the compression ring in the combustion chamber. GEN 49D with Anti-Gel now also provides all diesel engines with improved deposit control and improved low temperature fluidity.
Fuel Pump Anti-Wear
The addition of GEN 49D with Anti-Gel to #2 diesel fuel greatly improves the lubricity of the fuel. GEN 49D with Anti-Gel helps to protect critical pump vanes and plungers from wear. Two common standard tests are available to evaluate the lubricity of fuels.
BOCLE – The Ball On Cylinder Lubricity Evaluator (BOCLE) test wears a steel test ball against a rolling cylinder. The smaller the wear scar on the ball, the better the fuel’s lubricity. The pictures in Figure 1 show the significant reduction in the size of the wear scar in this lubricity test. GEN 49D with Anti-Gel improves the fuel lubricity by 10%.
HFRR – The newest test for diesel fuel specification testing is the High Frequency Reciprocating Rig (HFRR). In this test, a steel ball wears against a disk in high speed oscillation and the size of the wear scar is the measure of fuel lubricity.
The wear scar with GEN 49D with Anti-Gel treated fuel is over 40% smaller than the corresponding scar with the neat fuel. Photographs of the scars can be seen in Figure 2.
Inhibits Rust and Corrosion
The ASTM D665 corrosion test evaluates the tendency of fuel to cause fuel tank corrosion. The corrosion scale contributes to abrasive fuel pump wear. The photographs in Figure 3 show that the addition of GEN 49D with Anti-Gel reduces the amount of rust on the steel coupon.
In the ASTM D130 copper corrosion test the addition of 0.08% GEN 49D with Anti-Gel maintained the copper tarnish rating at 1a.
The data presented herein is accurate and obtained from the best information at the time of publication. Therefore, no legal liability is accepted by Power Up Lubricants, or any of its agents or affiliates, for the data, specifications or recommendations contained herein.
Kidco Gen 49D Evaluation
Date of Evaluation: July 3rd -24th, 2003
Location: Lafarge Spyhill Quarry, Calgary, Alberta
Job: Over Burden Removal/Fill
Kidco Construction Ltd. is constantly looking for ways to improve efficiency and to reduce operating expenses. One way of achieving these targets is through the use of Power Up Gen 49D diesel fuel additive. Added to diesel fuel at a ratio of 1:1200, this multifunctional additive not only reduces wear and friction in the fuel supply system, but also enhances combustion, ensuring that the bulk of the fuel is burned completely to carbon dioxide (CO2) and water in the cylinder. The benefits of this improvement are that more of the energy is captured to do useful work, thereby requiring less fuel to be burned, and a reduction in carbon monoxide (CO), partially burned fuel (HC), and soot particulates in the emissions. A superior, more uniform combustion front, as promoted by Gen 49D will also mean that the combustion will take place at a modest temperature, minimizing the formation of nitrogen oxides (NOx). The enhanced combustion inside the cylinder may also reduce exhaust gas temperatures, as the fuel is completely burned prior to reaching the exhaust system.
The test protocols set out required a base line data collection period of nine days to acquire statistically relevant data prior to implementation of Gen 49D. Data collected prior to and during the testing with Gen 49D included fuel consumption in liters, hours worked as recorded by the hour meter on each piece of equipment, and exhaust temperature recorded with a digital thermometer acquired from the Maryn Research Lab. Emission data was also collected using the Maryn, EA1020 five gas exhaust analyzer. The field evaluation included 4 pieces of Kidco equipment: 3 of which were scrapers (Unit # 294, 295 and 296) with the final unit being a caterpillar (Unit # 109). Following the initial data collection, 2 liters of Power Up Gen 49D were added to a 2400 liter fuel tank at the card lock fueling station. The fuel treated with Gen 49D was then delivered to the previously mentioned pieces of equipment.
Improvements in fuel economy for the evaluated equipment were substantial. Average consumption for the 4 pieces of equipment equated to 10.35%, a sum which significantly outweighed the cost of the Power Up Gen 49D added to the diesel fuel. In addition to fuel savings, recorded temperatures showed a 5.08% reduction in exhaust temperature at the manifold. Further benefits and advantages of Power Up Gen 49D will be evidenced through reduction in fuel pump and injector problems over the life of the equipment. While emission data was collected, at the present time the data has yet to be analyzed, therefore the final report is not yet ready for distribution.
While the recorded improvements are impressive enough on their own, by prorating these results over the entire Kidco fleet for one year we calculate that the annual net savings would be in excess of $500,000.
Mark Bishop
Managing Director
Maryn International Ltd.
July 29, 2003
Fuel Savings Presentation